Various processes are applicable according to the type and quantity of parts to be manufactured
Two major ways arise :
Features | Benefits | Disadvantages | |
---|---|---|---|
Non-permanents moulds | The mould is destroyed to pull out the part | Prototype and pilot series of parts manufacturing | Limited manufacturing rate The time to make the mould is higher than the time to cast |
Permanent moulds | The mould often in metal is reused to make several series of parts | Mass production rate Dimensional stability of produced parts | Possible part shapes are more limited because the part needs to be extracted from the mould |
Die-cast moulding (process used at DEJOIE) :
- Permanent mould, mainly made of steel, alloy cast with a ladle
- Series of several thousand parts
- The parts show a good surface quality
- The parts show good mechanical properties
Die-casting :
- Similar to die casting moulding except that the alloy is injected into the mould through a piston or a cylinder
- This technology is used for mass production
- The parts show a good surface quality
- Possibility to manufacture thin-walled parts
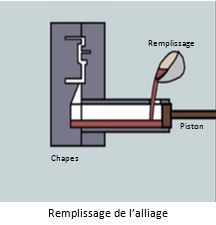

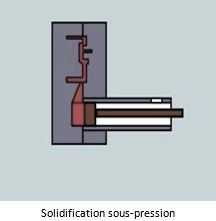
Sand casting :
- Moulding of a model or pattern plate in frames full with sand and alloy casting in the cavity left by the model
- Capacity to manufacture large and complex parts with holes thanks to the use of cores in the mould
- Applicable for prototyping, from a few to several hundreds of units
- Medium surface quality and medium dimensional precision
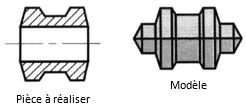
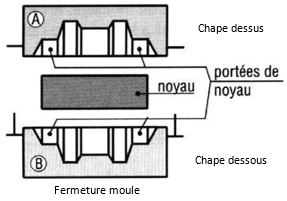
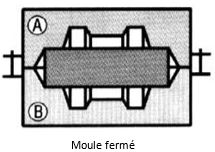
Practical advice for designing parts througbh die casting moulding :
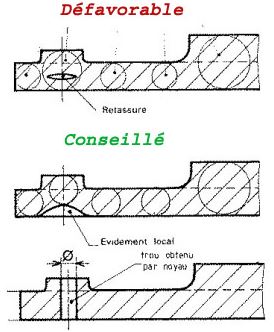
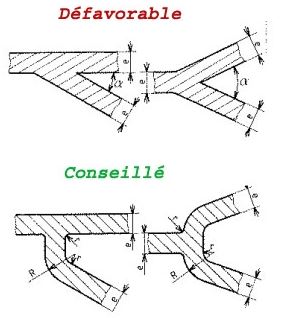
Avoid isolated masses
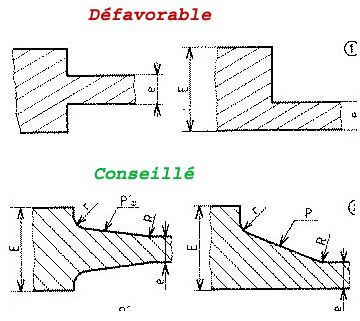
Avoid variations in part thickness, favour a molten alloy path
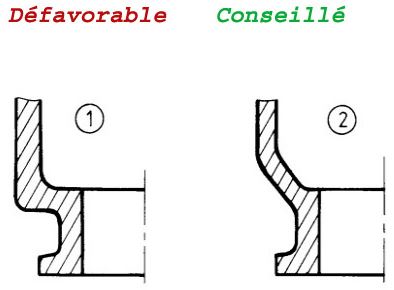
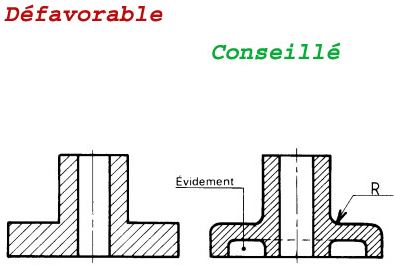
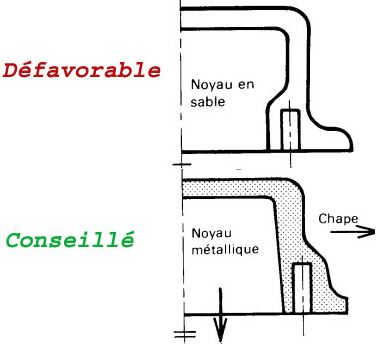
Avoid useless masses